Book Downloads Hub Reads Ebooks Online eBook Librarys Digital Books Store Download Book Pdfs Bookworm Downloads Free Books Downloads Epub Book Collection Pdf Book Vault Read and Download Books Open Source Book Library Best Book Downloads Dan Daly Michael Pearl Michael J Bradley Dove Winters Jillian Dodd Kim M Russell Alan Lawrence Sitomer Larry Degaris
Do you want to contribute by writing guest posts on this blog?
Please contact us and send us a resume of previous articles that you have written.
The Evolution Of The Toyota Production System Studies In Economic History

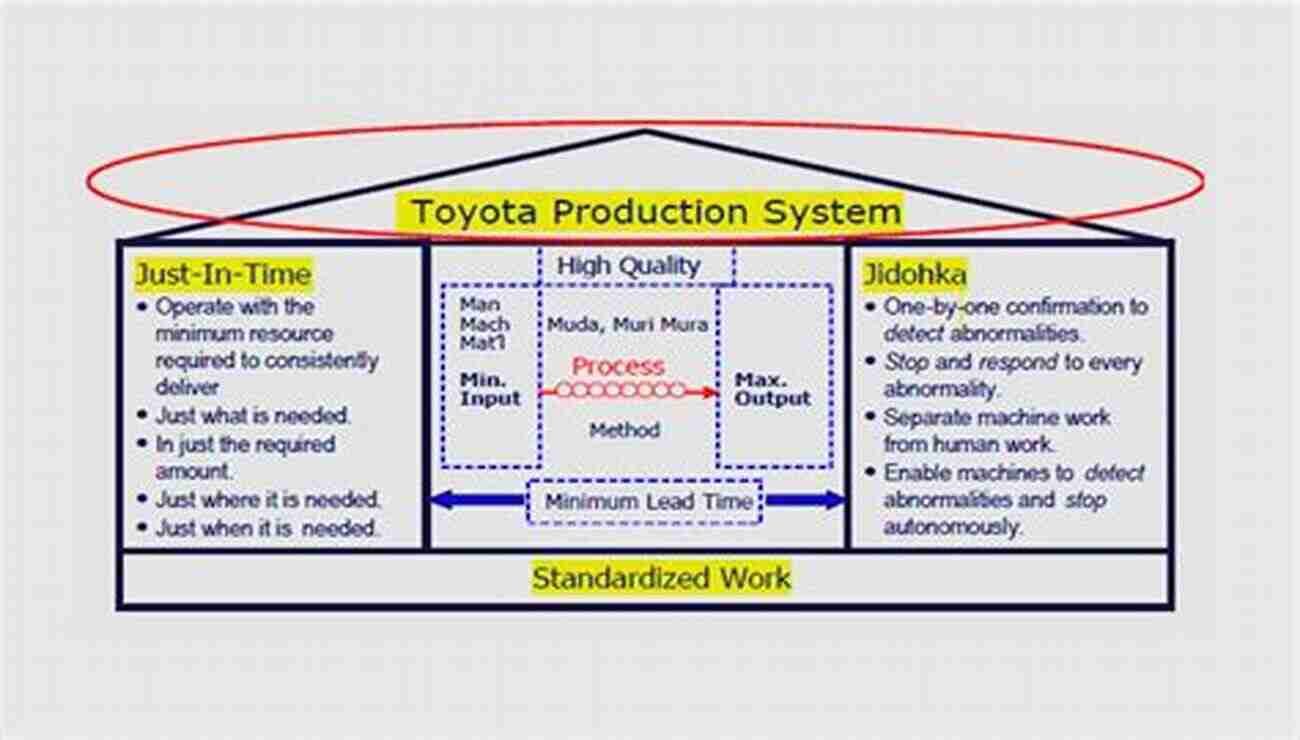
The Toyota Production System (TPS) is widely recognized as one of the most efficient and influential manufacturing systems in the world. It has revolutionized the automotive industry and set a benchmark for lean production techniques. This article explores the evolution of the Toyota Production System through the lens of economic history and discusses its impact on the global manufacturing landscape.
Origins of the Toyota Production System
In the mid-20th century, Japan was recovering from the devastating effects of World War II. Resources were scarce, and companies needed to find innovative ways to maximize productivity while minimizing waste. Toyota, under the leadership of Taiichi Ohno and Eiji Toyoda, developed the TPS as a response to these challenges.
The foundation of the TPS lies in two key principles: Just-in-Time (JIT) production and the concept of Kaizen, which focuses on continuous improvement. JIT production aims to minimize inventory levels and ensure that components and materials are delivered exactly when needed, reducing storage costs and increasing production efficiency.
4.6 out of 5
Language | : | English |
File size | : | 5684 KB |
Text-to-Speech | : | Enabled |
Enhanced typesetting | : | Enabled |
Word Wise | : | Enabled |
Print length | : | 311 pages |
Screen Reader | : | Supported |
The Lean Manufacturing Revolution
The TPS quickly gained recognition for its effectiveness, and other manufacturers around the world sought to replicate its success. The principles of the TPS formed the basis of what is now known as lean manufacturing—a philosophy that aims to eliminate waste and maximize value. Lean manufacturing has become a cornerstone of modern industrial practices, revolutionizing industries beyond automotive manufacturing.
The success of the TPS and lean manufacturing techniques can be attributed to several factors. Firstly, the emphasis on continuous improvement encourages employees at all levels to identify and eliminate waste, leading to greater efficiency and cost reduction. Secondly, the TPS promotes a culture of respect for people, creating a work environment that values employees' input and fosters teamwork.
Adapting to Changing Times
As technology and market dynamics have evolved, so too has the Toyota Production System. Toyota has continuously adapted its production processes to remain competitive and address emerging challenges. For example, the of automation and robotics has increased efficiency, reduced human error, and enabled higher quality standards. Additionally, Toyota has incorporated environmental sustainability practices into its production system, such as recycling and waste reduction initiatives.
The TPS continues to evolve, incorporating digital technologies, data analytics, and artificial intelligence to further optimize production processes. These advancements have allowed for greater customization, shorter lead times, and improved overall quality.
Impact on the Global Manufacturing Landscape
The Toyota Production System's influence extends far beyond the automotive industry. By demonstrating the effectiveness of lean manufacturing principles, Toyota has inspired countless companies across various sectors to adopt similar methods. Manufacturers around the world have implemented the TPS to increase productivity, reduce costs, and enhance overall performance.
The success of the TPS has also highlighted the importance of inter-firm collaboration and supplier integration. The system encourages partnerships between Toyota and its suppliers, promoting mutual trust and shared goals. This collaborative approach has proven effective in reducing waste, optimizing supply chains, and ensuring high product quality.
The evolution of the Toyota Production System is a testament to the power of continuous improvement and innovation. What started as a response to post-war challenges has transformed into a global benchmark for efficient manufacturing. Through its emphasis on waste reduction and value maximization, the TPS has not only revolutionized the automotive industry but also influenced manufacturing practices across diverse sectors. As technology continues to advance, the TPS will undoubtedly continue to evolve, shaping the future of manufacturing for years to come.
4.6 out of 5
Language | : | English |
File size | : | 5684 KB |
Text-to-Speech | : | Enabled |
Enhanced typesetting | : | Enabled |
Word Wise | : | Enabled |
Print length | : | 311 pages |
Screen Reader | : | Supported |
This book utilizes historical evidence to describe the development of the Toyota Production System (TPS). The development of TPS typifies the transformation of production control in interchangeable industries in the twentieth century. Much of the extensive literature available on TPS has been geared toward describing TPS from a number of different perspectives. Many researchers consider TPS distinct from American mass-production systems. Although TPS (and, more generally, the production control systems in the Japanese assembly industry) has differentiated itself from similar US production systems, the evolution of TPS is largely attributable to attempts to learn from, imitate, and modify pre-World War II US production methods. Through these efforts, TPS has achieved levels of efficiency in Japan comparable to those of US production systems. Additionally, a reliance on Information and Communication Technology (ICT) in relation to production control has facilitated the development of TPS. The literature on TPS, however, has largely ignored the vital relationship between ICT and production control due to an inordinate focus on “Kanban.” Kanban translates to “signboard” in Japanese but is used to refer to an organic linkage between work in preceding and subsequent production processes. This book sheds light on the development of a fully digitalized Bill of Materials (BOM) at Toyota, behind its Kanban and production control.
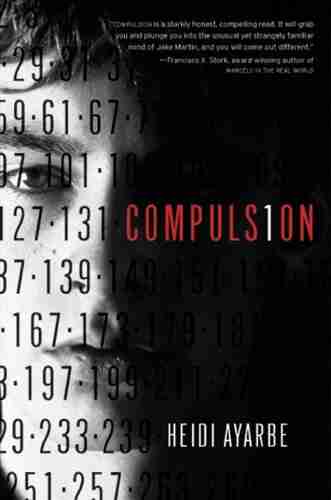

Compulsion Heidi Ayarbe - A Gripping Tale of Addiction...
Compulsion Heidi Ayarbe...


The Cottonmouth Club Novel - Uncovering the Secrets of a...
Welcome to the dark and twisted world of...
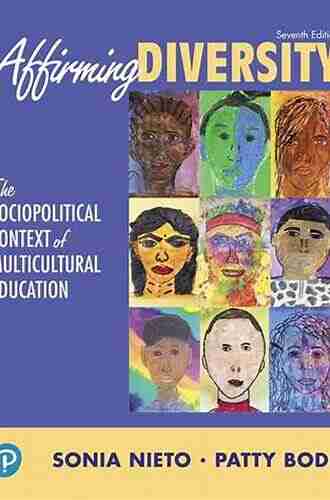

The Sociopolitical Context Of Multicultural Education...
Living in a diverse and interconnected world,...
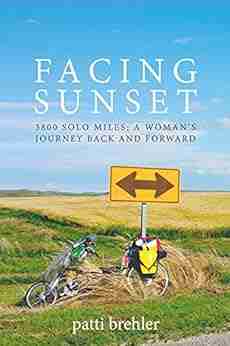

The Epic Journey of a Woman: 3800 Solo Miles Back and...
Embarking on a solo journey is a...
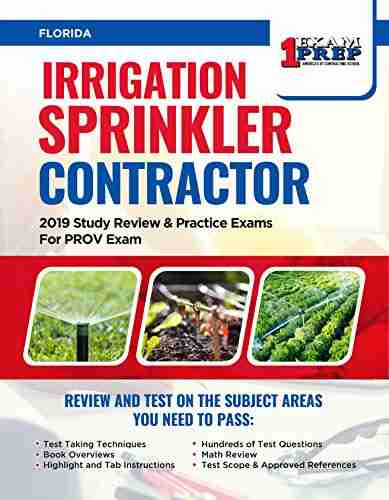

Florida Irrigation Sprinkler Contractor: Revolutionizing...
Florida, known for its beautiful...
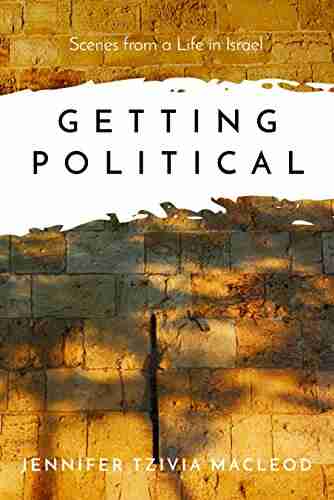

Unveiling the Political Tapestry: Life in Israel
Israel, a vibrant country located in the...
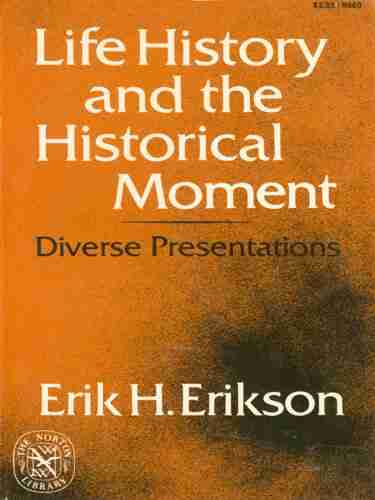

Life History And The Historical Moment Diverse...
Do you ever find yourself...
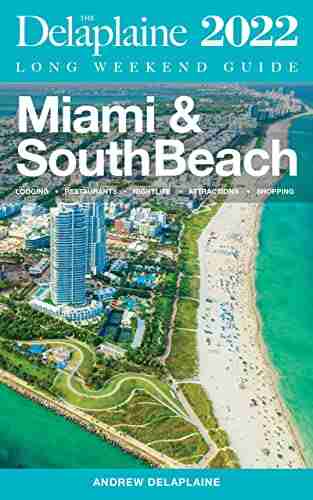

Miami South Beach The Delaplaine 2022 Long Weekend Guide
Welcome to the ultimate guide for...
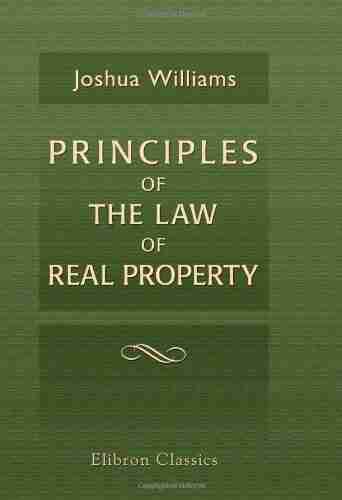

An In-depth Look into the Principles of the Law of Real...
The principles of the...
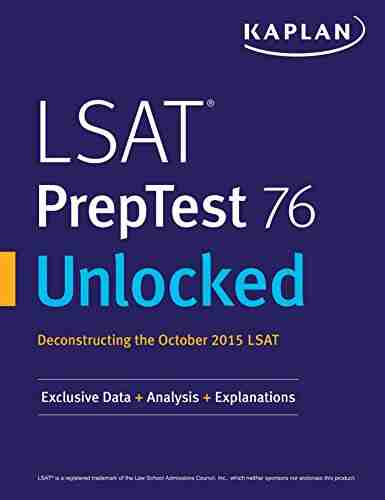

Exclusive Data Analysis Explanations For The October 2015...
Are you preparing for the Law School...
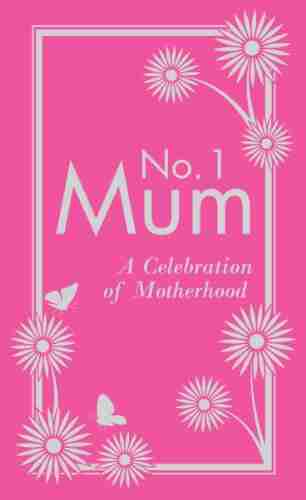

The Secret to Enjoying Motherhood: No Mum Celebration of...
Being a mother is a truly remarkable...
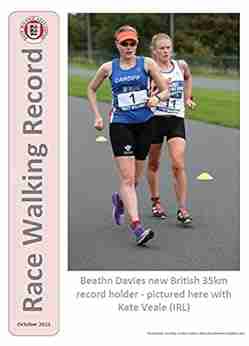

Race Walking Record 913 October 2021
Are you ready for an...
Light bulbAdvertise smarter! Our strategic ad space ensures maximum exposure. Reserve your spot today!
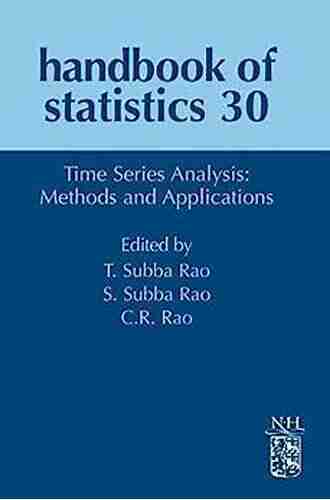

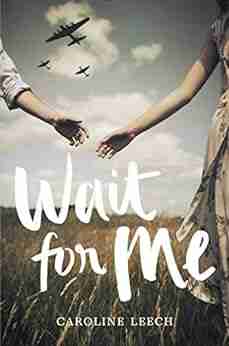

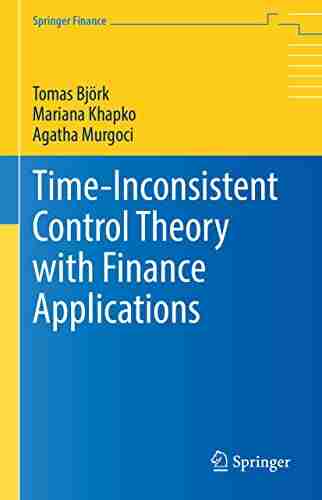

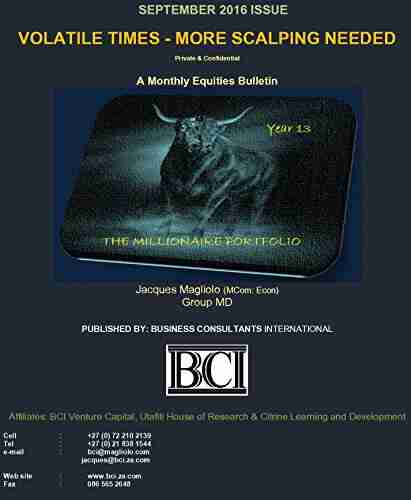

- Dominic SimmonsFollow ·18.5k
- Earl WilliamsFollow ·12.5k
- Amir SimmonsFollow ·2.3k
- Theo CoxFollow ·11.5k
- Wade CoxFollow ·16.3k
- Darrell PowellFollow ·10.8k
- J.D. SalingerFollow ·19k
- Mark TwainFollow ·9.6k