Book Downloads Hub Reads Ebooks Online eBook Librarys Digital Books Store Download Book Pdfs Bookworm Downloads Free Books Downloads Epub Book Collection Pdf Book Vault Read and Download Books Open Source Book Library Best Book Downloads John Richardson Noo Saro Wiwa Marisa Silva Dawn Maslar Nora Leary Taj Mccoy El Christen Brown William Mckeever
Do you want to contribute by writing guest posts on this blog?
Please contact us and send us a resume of previous articles that you have written.
Unlocking Success: A Practical Approach to Lean Six Sigma

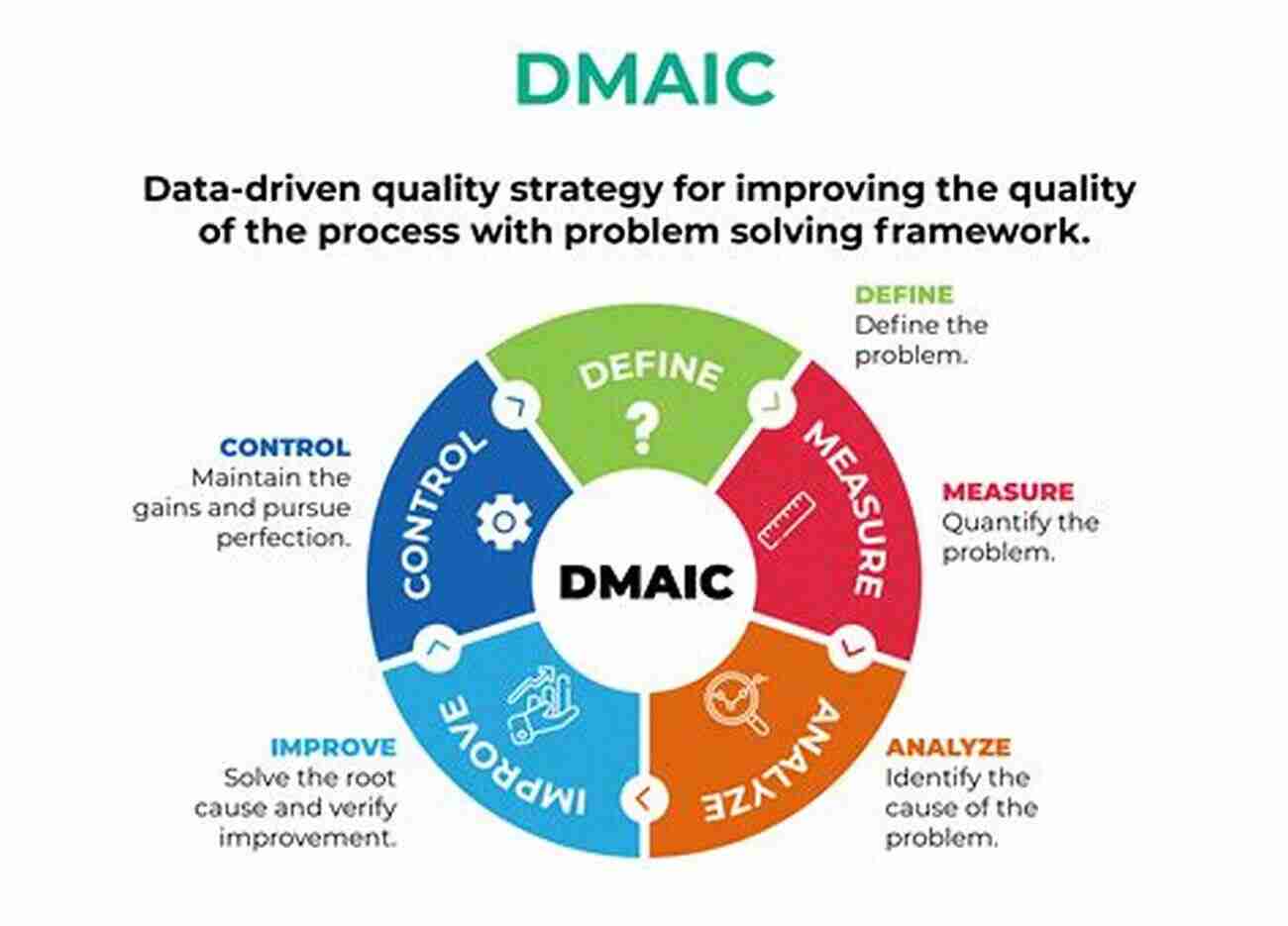
In today's fast-paced and highly competitive business environment, organizations are constantly looking for ways to improve their processes and reduce waste. Lean Six Sigma has emerged as a powerful methodology to achieve this goal. Combining Lean principles, which focus on eliminating waste, with Six Sigma's data-driven approach to reducing defects, Lean Six Sigma has proven to be a valuable tool for organizations of all sizes and industries.
What is Lean Six Sigma?
Lean Six Sigma is a management approach that aims to improve efficiency and quality by identifying and eliminating waste and reducing variability in processes. It combines the Lean principles, developed by Toyota, with Six Sigma's statistical tools and techniques. The main objective of Lean Six Sigma is to improve customer satisfaction, reduce costs, and increase overall operational efficiency.
The Practical Approach
Implementing Lean Six Sigma can be a daunting task, but by adopting a practical approach, organizations can overcome challenges and achieve long-term success. Here are the key steps to a practical Lean Six Sigma implementation:
4.3 out of 5
Language | : | English |
File size | : | 21448 KB |
Text-to-Speech | : | Enabled |
Screen Reader | : | Supported |
Enhanced typesetting | : | Enabled |
Word Wise | : | Enabled |
Print length | : | 520 pages |
Lending | : | Enabled |
Step 1: Define the Problem
The first step in Lean Six Sigma is to clearly define the problem or opportunity for improvement. This involves understanding the current state, identifying pain points, and setting measurable goals. A well-defined problem statement provides a clear direction for the project and helps in identifying the appropriate tools and techniques.
Step 2: Measure the Process
Once the problem is defined, it is important to measure the process using relevant data. This involves collecting and analyzing data to understand the current performance of the process and identify areas of improvement. Statistical tools are used to analyze the data and identify the root causes of defects or waste.
Step 3: Analyze the Data
After measuring the process, it's time to analyze the data and identify patterns, trends, and potential causes of waste or defects. This step involves applying various statistical tools and techniques, such as Pareto analysis, histogram, scatter plot, and fishbone diagram, to gain insights into the process and identify improvement opportunities.
Step 4: Improve the Process
Based on the analysis, organizations can now develop and implement improvement solutions. This involves brainstorming, evaluating alternative solutions, and selecting the most feasible and effective one. Lean Six Sigma provides a structured approach to process improvement and encourages the involvement of cross-functional teams to drive change.
Step 5: Control the Process
Once the process has been improved, it is crucial to establish control measures to sustain the improvements. This involves developing standard operating procedures, training employees, and implementing monitoring systems to ensure that the process stays within the desired performance levels. Ongoing monitoring and periodic review of the process are essential to prevent any deviation or regression.
The Benefits of Lean Six Sigma
Implementing Lean Six Sigma can bring numerous benefits to organizations, including:
- Reduced process inefficiencies and waste
- Increased customer satisfaction and loyalty
- Improved product/service quality
- Enhanced employee engagement and teamwork
- Reduced costs and increased profitability
- Streamlined processes and improved operational efficiency
Lean Six Sigma provides a practical and systematic approach to process improvement, enabling organizations to achieve operational excellence and improve overall performance. By leveraging the combination of Lean principles and Six Sigma tools, businesses can streamline their operations, reduce waste, and enhance customer satisfaction. With proper planning, execution, and control, Lean Six Sigma can unlock success and create a competitive edge in today's business landscape.
4.3 out of 5
Language | : | English |
File size | : | 21448 KB |
Text-to-Speech | : | Enabled |
Screen Reader | : | Supported |
Enhanced typesetting | : | Enabled |
Word Wise | : | Enabled |
Print length | : | 520 pages |
Lending | : | Enabled |
Lean Six Sigma for Service - Pursuing Perfect Service is a comprehensive and detailed set of instructions on how to implement Lean and Six Sigma tools and concepts in a variety of environments. This revised edition contains over 40 Dropbox file links to Excel worksheets for immediate application of the tool or concept. This book provides a solid foundation upon which Lean Sigma tools can be applied in any service organization. Service providers are continually processing daily requests and must know how to identify client needs and expectations, how to best satisfy their needs, and how to do it at the lowest possible cost. This book is a step-by-step implementation guide for continuous improvement while creating a solid foundation upon which to build a service excellence culture. Pursuing Perfect Service also provides insights and examples on how Information Technology can be used to improve data and information flow to enhance the overall client experience, while ensuring organizational profitability. This book has been arranged into four distinct parts. To transform an organization from a traditional service provider to a Lean Sigma for Service Excellence provider, it is recommended that the book be followed in order, from Part One to Part Four. However, it may be useful to review Chapter 10, Transformation Case Study, as it chronicles one company's journey using this approach or methodology. The four parts are: Part One. Setting the Foundation for Lean Sigma for Service Excellence, Part Two. Beginning the Lean Sigma for Service Excellence Journey, Part Three. Deploying the Lean Sigma for Service Excellence Improvement Process and Part Four. Putting it All Together to Achieve and Sustain Lean Sigma for Service Excellence. The Lean Six Sigma for Assessment and Gap Analysis has also been provided as a Dropbox file link to the Excel worksheet for creating a baseline for your organization. Don't go Lean without this complete book of steps for implementation, case study examples of Lean Six Sigma, and all the Excel worksheets for you to customize and use.
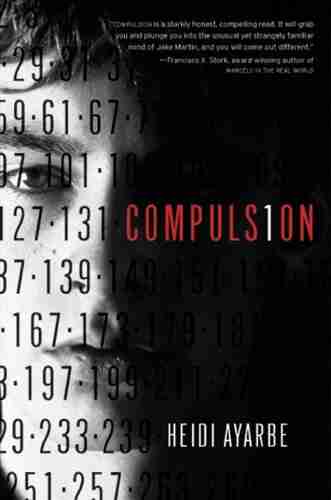

Compulsion Heidi Ayarbe - A Gripping Tale of Addiction...
Compulsion Heidi Ayarbe...


The Cottonmouth Club Novel - Uncovering the Secrets of a...
Welcome to the dark and twisted world of...
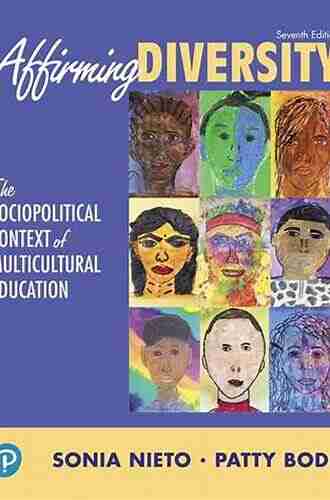

The Sociopolitical Context Of Multicultural Education...
Living in a diverse and interconnected world,...
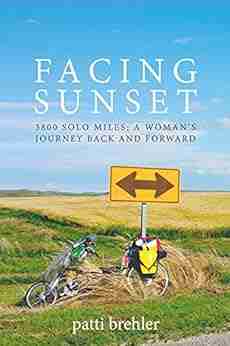

The Epic Journey of a Woman: 3800 Solo Miles Back and...
Embarking on a solo journey is a...
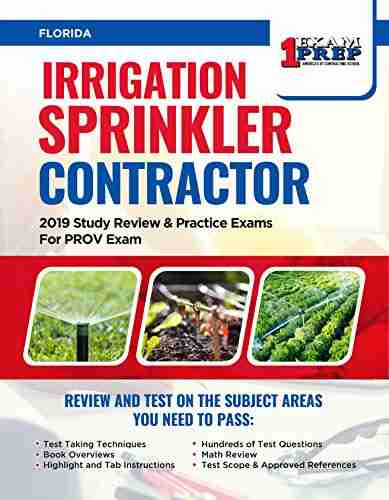

Florida Irrigation Sprinkler Contractor: Revolutionizing...
Florida, known for its beautiful...
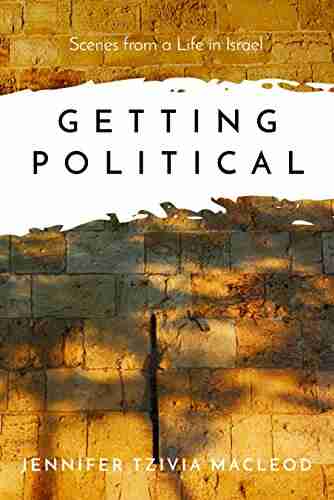

Unveiling the Political Tapestry: Life in Israel
Israel, a vibrant country located in the...
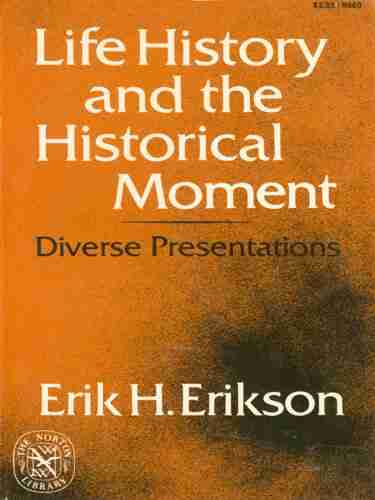

Life History And The Historical Moment Diverse...
Do you ever find yourself...
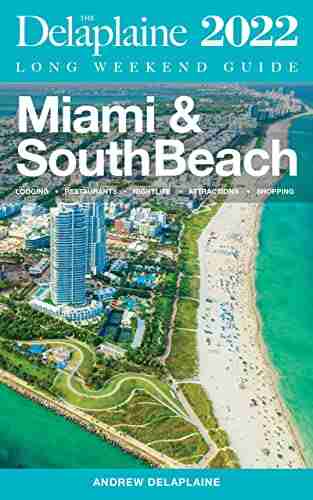

Miami South Beach The Delaplaine 2022 Long Weekend Guide
Welcome to the ultimate guide for...
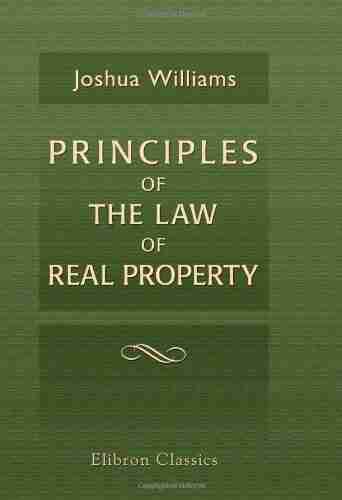

An In-depth Look into the Principles of the Law of Real...
The principles of the...
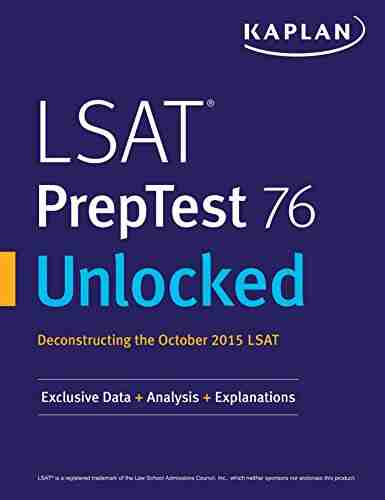

Exclusive Data Analysis Explanations For The October 2015...
Are you preparing for the Law School...
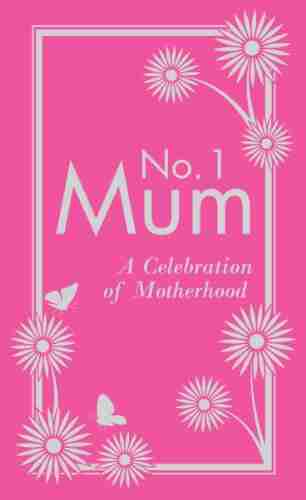

The Secret to Enjoying Motherhood: No Mum Celebration of...
Being a mother is a truly remarkable...
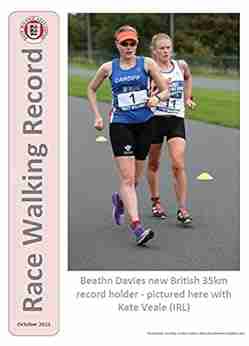

Race Walking Record 913 October 2021
Are you ready for an...
Light bulbAdvertise smarter! Our strategic ad space ensures maximum exposure. Reserve your spot today!
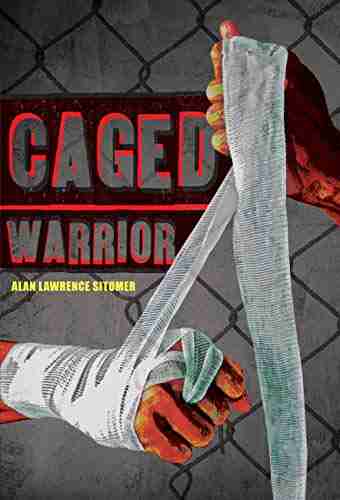

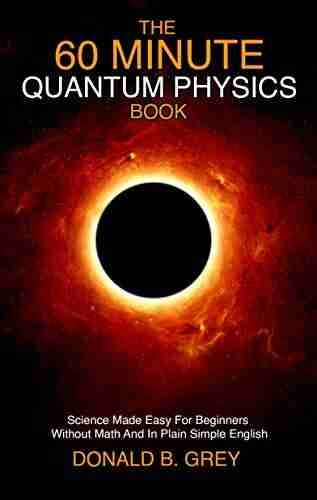

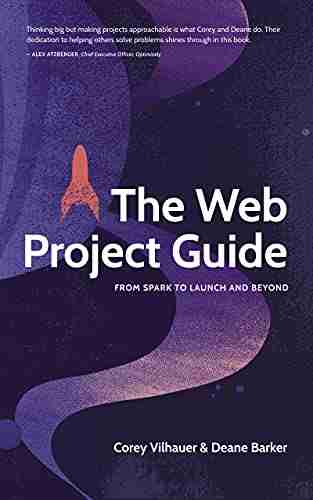

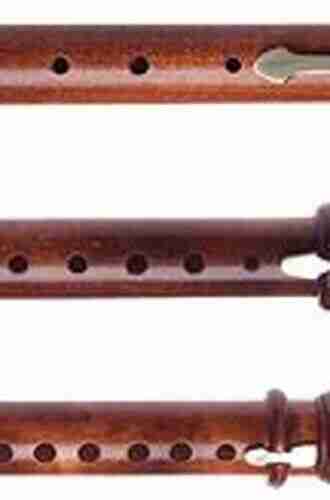

- Abe MitchellFollow ·19.8k
- Thomas PynchonFollow ·17.9k
- Dakota PowellFollow ·12.3k
- Floyd PowellFollow ·11k
- Jimmy ButlerFollow ·15k
- Spencer PowellFollow ·15.3k
- Nathan ReedFollow ·7.4k
- Mario BenedettiFollow ·17k